Maximizing Robotic Arc Welding System ROI
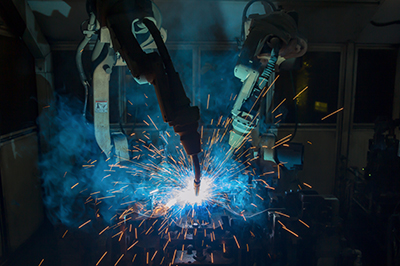
Higher product quality, productivity requirements, and reduced costs have pushed manufacturers to seek out a robotic welding system that can meet their needs. Robotic welding processes offer attractive solutions over traditional manual operation and hard automation.
Since the 1960s, robotic welding systems have found their way into a broad range of industrial sectors. As a result, robotic welding has been recognized as the most popular application of robotics worldwide. Automotive manufacturing is the most active sector for robotic welding, but the agricultural and general industries also make extensive use of the technology.
Basics of a Robotic Arc Welding System
A robotic arc welding system is the combination of two subsystems: the welding equipment delivering energy from the welding power source to the workpiece, and the robot that provides positioning of the heat source and the workpiece. Six-axis welding robots often use a three-axis arm and three-axis wrist, with the welding torch mounted at the end, to achieve all positions needed for three-dimensional welding.
In a production environment, workpiece manipulators are often implemented as part of the system. The devices not only help to improve the welding robot’s range, but also accessibility. The control manipulator is integrated with the robot and allows for synchronized and simultaneous control of the two systems.
Maximizing ROI with Robotic Welding Systems
Automation is only considered successful if there is an increase in return on investment. Three key areas where manufacturers need to see ROI include part repeatability, maintenance, and training. Here’s why ROI in these areas is so important.
Part Repeatability
The quality of a part produced within a robotic welding system depends on the quality of the part that enters the robotic weld cell. If the part enters flawed, the weld will be flawed as well. Thus, the time and investment behind performing the robotic weld will be wasted. Proper fixturing, which not strictly “robotics”, is important to part repeatability as well — parts must be held in exact positions during the welding process.
Training
Robotic welding systems need properly trained operators to control them. A skilled welding operator or an individual with previous welding management experience is usually best for the job. A trusted robotic integrator can help to provide training on programming, troubleshooting, and preventative maintenance.
Certified Robotic Arc Welding (CRAW) courses offer plenty of hands-on training. Over four days, 80% of class time is hands-on with the teach pendant. The course covers an extensive list of topics, including welding safety, shielding gas selection, troubleshooting welding problems, and determining weld size limits.
Maintenance
To protect their investment, manufacturers must perform regular maintenance. Neglecting maintenance can lead to unscheduled downtime, poor quality parts, costly repairs and, in extreme cases, full equipment replacement.
Empower your operators to maximize productivity with the latest knowledge in robotics Ask about robotic training by seasoned professionals offered by Genesis Systems, IPG Photonics Company, at their Davenport, Iowa state-of-the-art facility.
Posted in Robotic Welding