What is Resistance Welding and What are the Different Types?
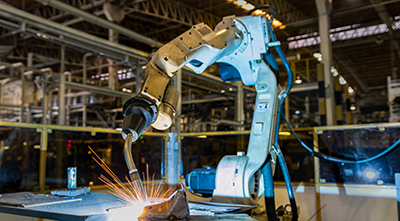
In the simplest terms, resistance welding is joining metals with pressure and electrical current. But complex automation systems transform resistance welding into a process that can speed up welding projects with exceptional accuracy. This potential for faster welding processes is why industries are so keen on bringing this technology to the manufacturing process.
A Resistance Welding Primer
Resistance welding involves joining metals by first applying pressure to two or more metal components. Electrical current is then passed through the metals for a precise length of time. No other materials are needed to weld the two components together. The metals are then melted and fused in a clean, fast, and cost-effective process.
There are several types of resistance welding processes, including spot-and-seam, flash, projection, and upset welding. The most significant differences between these methods are the types and shapes of the electrodes used to apply the pressure and the electrical current. Water flows through cavities inside the electrode and other tools for cooling.
Spot welding is the simplest form of resistance welding. The electrodes apply both the pressure and the force to the components to be welded. Seam welding is similar to spot welding except that the components to be welded roll between wheel-shaped electrodes while a current is applied. These welds often overlap, resulting in a welded seam instead of spot welds.
Flash welding uses force to push workpieces together. A flashing action created with a high current density at very small contact points expels oxides and impurities, resulting in a stronger weld. Upset welding is similar to flash welding, but the components are already in firm contact and, thus, no flashing occurs. Projection welding localizes welds at predetermined points by use of projections that focus heat generation at the point of contact. Sufficient resistance causes the projections to collapse and the weld nugget is formed.
Resistance Welding Offers Many Advantages
Robotic resistance welding increases throughput, reduces process times, and results in a better-quality weld. Resistance welding is faster than fastening components together by the use of riveting and offers more shear resistance. Compared to other fastening and welding methods, resistance welding reduces the chance of workpiece deformation.
Resistance welding can be performed with single-phase AC power, making it an accessible form of joining workpieces. It’s also available in mid-frequency DC voltages, which can increase energy efficiency and increase quality further. Projection welding offers an excellent solution for nut and bolt welding. Spot welding is especially useful for sheet metal applications, where three or more metals’ thickness can be welded together simultaneously.
Take advantage of Genesis’s free ebook to gain helpful insights. Download the free ebook 6 Business Considerations for Robotic Welding Investments.
Posted in Robotic Welding