Case Study – NSpect 216
Genesis Case Study #: J8223_001
Application: Robotic Non-Destructive Inspection
Market Segment: Aerospace
Product: Composite Rocket Components
Cycletime: > 2 Hours per Part
Need assistance choosing the right system?
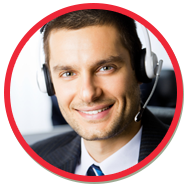
Give us a call and one of our knowledgeable sales representatives will help!
563-445-5600Request a Quote:
Get a Quote for the Case Study – NSpect 216
Download the NSpect 216 Case Study PDF
Summary
Large payload fairing (≈40 ft long x 18 ft across) is loaded on 4 support beams 12 ft from the ground. Robot and track are underneath part. Operator selects robot program name from HMI and cycle starts the machine. The PLC sends the part information to a NDI acquisition PC located on the robot carriage via an Ethernet socket. Robot starts program by handshaking to the NDI PC via an Ethernet socket. Once handshaking is complete the robot feeds the large yoke onto the part and starts jogging down the track while triggering the NDI PC to take data. At the end of each scan line (jog down the track) the robot and PC handshake again and the robot indexes ≈1mm further onto the part. After scanning the whole part the robot handshakes a scan complete and jogs to a home position based on the yoke size. There is also a turntable which spins in a ‘washing machine’ motion to scan a cylindrical part.
Project Challenges
- Yoke design/size/weight/stability
- Noise on TTL trigger line/array signal lines
- Turntable rotation and triggering
Genesis Solution
- Specially designed carbon fiber yokes for weight reduction and stability
- Triax trigger cable, opto-isolator on trigger line, placed Sonda pulse/receiver on carriage to shorten trigger/array lines
centerline of the turntable face to provide distance traveled during rotation (distance from center required in calculation)