Future Trends in Aerospace Automation
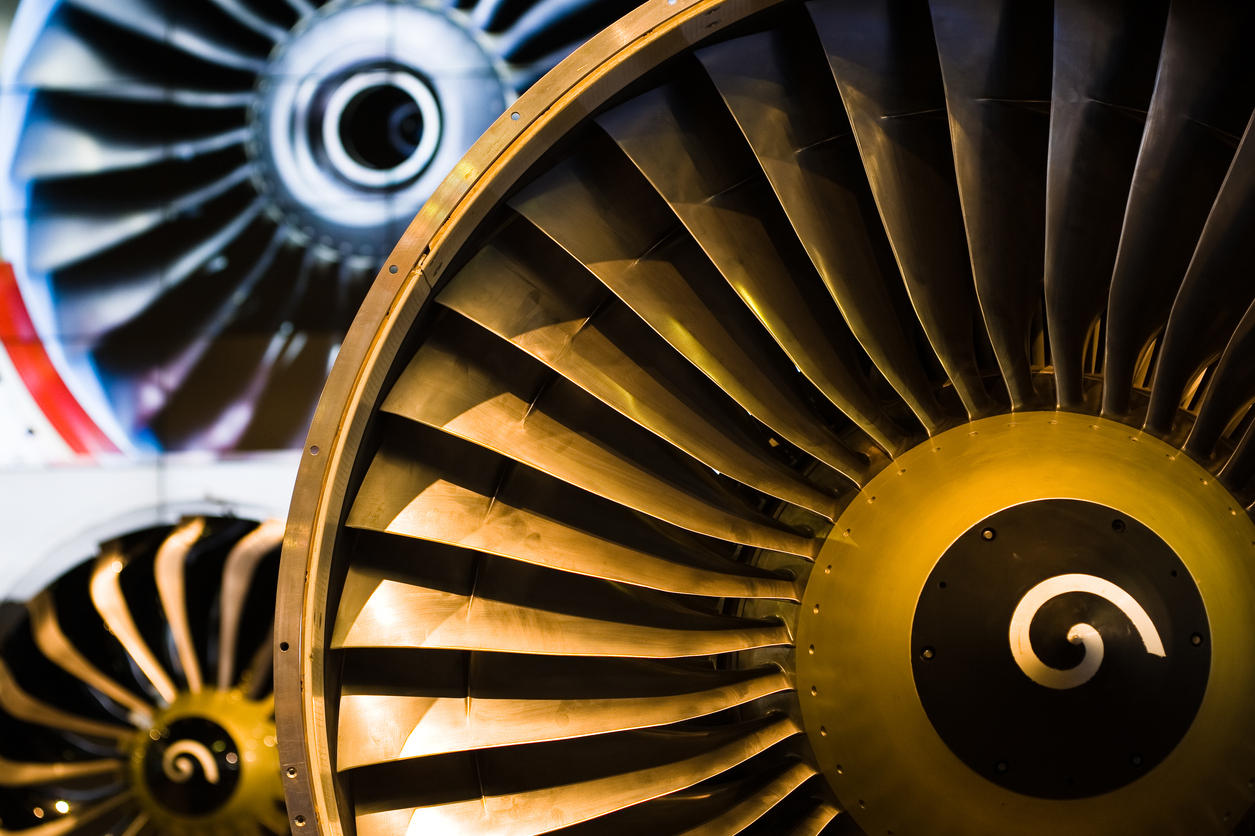
The aerospace industry keeps growing and manufacturers are searching for innovative ways to ramp up production. The challenge is that airplanes are complex, highly engineered machines and their components must be manufactured with an extremely high degree of accuracy. Advances in robotic integration solutions are helping the aerospace industry to overcome these challenges.
Aerospace Automation Offers Promise
The aircraft production process offers high potential for automation. Robotics can fill the needs of fabrication jobs like carbon fiber layup, trimming, routing, and drilling. Robots can also do assembly jobs such as fastening, sealing, and painting. They are also now used to inspect aircraft, a very time-intensive process due to strict standards required of the aircraft industry.
Automation Handles More Capacity
The large size and weight of aircraft parts pose another challenge. Workers, and now robots, must be able to position large, heavy components used during assembly of the fuselage and wings. Thanks to automation tech, some of the largest parts are moved around on Automated Guided Vehicles (AGVs). The robots are then moved into place and get to work. End effectors, the part of robots that interact with the environment, keep scaling up their capacities to handle higher loads to manipulate the heavy aircraft components.
One area where automation has proved greatly beneficial is in the drilling and fastening of thousands of rivets that hold together an airplane. New end effectors are designed with the ability to switch drills and fasteners depending on the size of the hole required. Advanced systems let two robots work in unison, one outside the fuselage to drill and install the rivets, and one inside to hold and stabilize the rivet, saving production time.
Aerospace Automation Make Work Environments Safer
Robots are performing repetitive work that causes injury to humans, saving a company costs due to labor and production losses. The installation of thousands of rivets was once handled by a two-person team. The repetitive work put considerable stress on the shoulders, back, arms, and elbows.
Robots are also handling hazardous tasks like the xenon flash laser ablation process used for surface paint removal. Robots are also used in confined spaces instead of sending humans into these hazardous areas. Humans can also be removed from environments where there is movement of heavy machinery and construction materials.
Manufacturing Cells Get More Flexible
Advancements in technology have allowed robotic manufacturing cells to accommodate a variety of parts instead of requiring dedicated cells for specific parts. This allows for less investment in machinery and tooling. Robotic solutions also offer increased position and path accuracy, helping manufacturers make better use of the space they have.
Robotic Solutions Become More Intelligent
Machine vision, force, and torque sensors now provide robots improved intelligence. The data gathered with cameras and sensors is interpreted by artificial intelligence. Machine learning lets robots carry out tasks that are increasingly complex. Operators are able to spend less time programming and teaching the robots to perform their functions thanks to new software packages.
Automation is providing aerospace manufacturers with the solutions they need to overcome the toughest production challenges – from design through inspection and testing. With continued technological advances and innovation, robotic integration is expanding to offer multi-process solutions that reduce costs, protect workers and speed production.
Learn how Genesis Systems automation solutions for aerospace & aircraft are helping manufacturers with their toughest manufacturing challenges.
Posted in Robotic Applications, Robotic Material Handling