Why Industrial & Collaborative Robot Safety Should Be a Top Priority
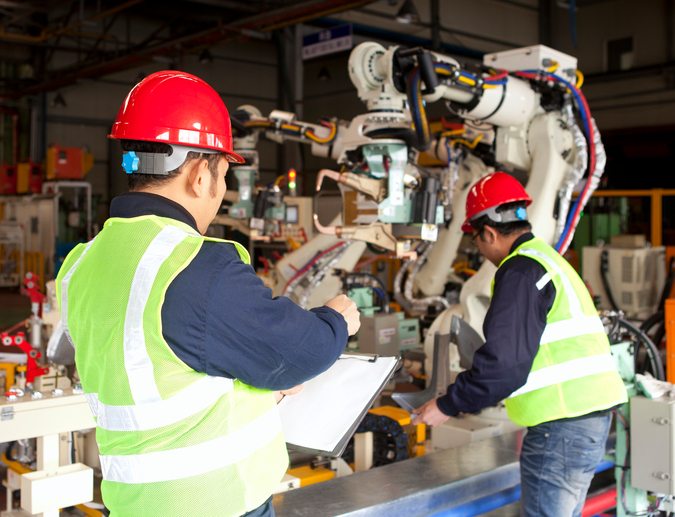
Industrial and collaborative robot safety should be a top priority in manufacturing facilities across the world. Robotic safety is about more than a legal requirement – it’s about safeguarding human lives and contributing to the overall productivity of automated production.
While robots are relatively safe – the Occupational Safety and Health Association (OSHA) identified only 27 fatalities associated with robots in a 30-year period between 1984 and 2013 – accidents still occur, and they can be costly in a number of ways.
Why is Robot Safety So Important for Manufacturers?
Industrial and collaborative robot safety is important for manufacturers for a wide range of reasons, but first and foremost is to protect workers from harm. No matter how automated a production process is, a human’s intelligence and problem-solving skills are indispensable. Laborers are a vital part of the production process, and manufacturers have a duty to protect them.
Further, safety can be leveraged as a productivity tool, too. Safety violations can lead to expensive fines. Accidents create expensive downtime, strain the labor force and can even damage automation equipment. In addition to protecting workers, safety should be a top priority for manufacturers because it’s closely linked with productivity and operational costs.
How to Improve Robot Safety in Your Factory
Fortunately, there are many different options manufacturers have to improve robot safety. All of these options can and should be implemented during the integration phase.
The most basic type of protection, mainly used for industrial robots, is protection on the outside of the robot or workcell. This could include hard-guarding like physical fences or safety latches that keep workers from nearing the robot during operation.
Another type of protection is inside protection features. These include features like collision detection sensors, which send an emergency halt signal when an abnormal force is detected. Safety sensors, whether they’re cameras or lasers, detect motion within a certain distance of a robot and can trigger an emergency shut down if a worker gets too close.
A third type of robot safety, and arguably the most important, is proper training. Your robot integrator should be able to provide all the necessary training for your staff. Fully understanding the dangers industrial and collaborative robots present, and how to minimize the risk of dangerous situations, can be the most effective safety procedure on your factory floor.
Industrial and collaborative robot safety should be a top priority for all manufacturers who leverage automation technology, not only to protect workers but to improve productivity. There are many options available for manufacturers to create a safe working environment.
A robot integrator plays an important role in creating workplace safety. For real-life examples of robot safety and productivity, browse our extensive library of robotic integration case studies to learn more on this subject.
Posted in Robot Safety