Robotic Workcell Design to Overcome the Challenges of Working with Large Parts
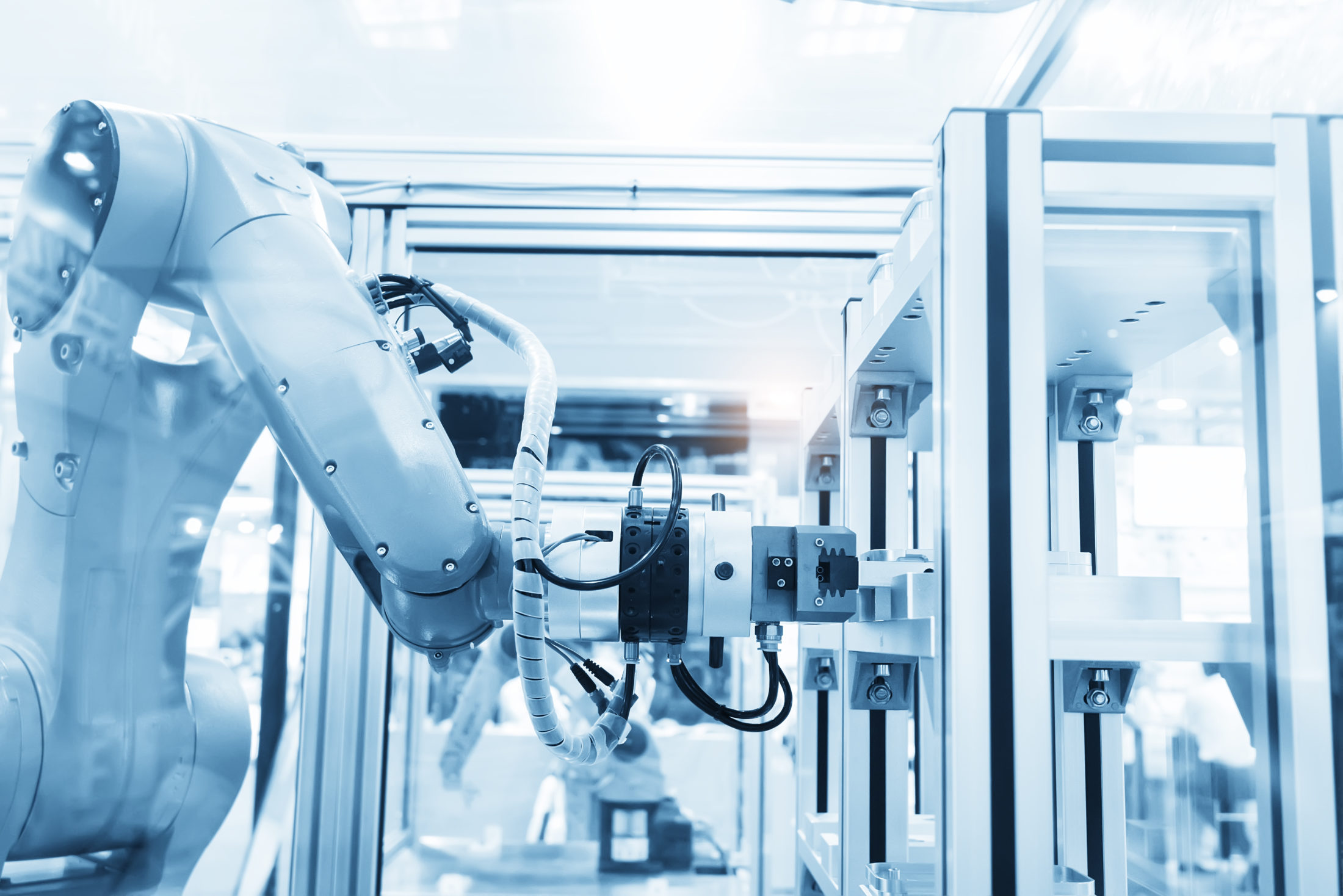
In robotic automation, large workpieces present numerous unique challenges for integrators and end users. Whether it’s robotic welding, machine tending, material handling, non-destructive inspection or any other form of robotic automation, working with large parts can pose several logistical challenges that don’t exist with smaller parts.
With smaller components, the primary focus is on how the robot will perform its basic functions. But with larger workpieces, new considerations come into play. How the robot will access the work area, how the workpiece will be physically moved, and how to increase the speed of processes to ensure return on investment (ROI), all need to be accounted for before a robot is installed.
How Robotic Workcell Design Accommodates Large Parts
Robotic workcells come in many shapes and forms. Custom solutions can accommodate practically any size part. One particular design aspect that enables working with large parts is servo track-mounted robots. This level of mobility gives a robot enhanced access to a part far beyond its standard reach, all while saving crucial floor space on the factory floor.
Workcell configuration also facilitates the processing of large parts. This could come in the form of multi-robot configurations that reduce the required mobility of each robot, as well as the part itself. It may also come in the form of advanced fixtures and positioners to move large workpieces for greater robot access.
When it comes to robot workcell design, there are many ways in which the challenges of working with large parts can be overcome.
Custom Robotic Tooling Cuts Lead Times for Tractor Cab Welding
A manufacturer of tractor cabs recently approached Genesis with a need to automate welding processes. They had a particular focus on the speed of production to help reduce the lead times of their tractor cabs.
Genesis integrated a custom workcell with a flow-through approach for material handling and two servo track mounted robots for optimal reach. Custom fixtures were designed and the entire workcell was programmed offline so it was ready to start welding the moment it was installed.
In the end, the manufacturer saw significantly increased throughput and faster production, cutting their lead time by 4 weeks.
To learn more about this topic, read the whole case study on this custom robotic welding workcell for a manufacturer of tractor cabs.
Posted in Robotic Applications