Laser Brazing Maximizes Material Removal Efforts in Aerospace Manufacturing
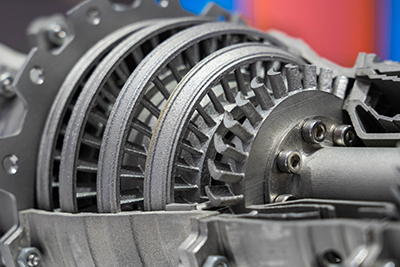
New advances in laser brazing make this cutting-edge technology even more useful for the aircraft, space, and defense industries. Until recent innovations, coated metals presented significant challenges to conventional brazing. However, new laser brazing methods and automated solutions let manufacturers join coated components faster.
You’ve likely heard of welding, but what’s the difference between that and brazing? Welding requires melting the base parts, while brazing joins the metal parts by the use of filler material. The filler flows into the joint and bonds the metal parts when it cools. Brazing can occur at a lower temperature than welding, so there’s less risk for distortion of the base parts.
Laser Brazing Further Speeds Up the Joining Process
With the adoption of fiber laser brazing technology, manufacturers were able to speed up the joining process. The laser is focused on the filler material and the joint. The precise, concentrated lasers eliminate the need to heat entire parts. Because less heat is used and flux isn’t needed, laser brazing is faster as there’s no need to wait for parts to cool.
Before laser brazing, most brazing methods required manual preparation of coated metals to join components. The joint first had to be stripped of any material coating so that the filler could properly bond to the base metals. This process required a lot of worker hours, but it was later found that the lasers used to heat the brazing filler material could perform double duty.
This discovery was perfect for brazing hot-dip galvanized sheets. At high speeds, micro-splashes and wavelets form. But now the laser first ablates the coated surface of the metal parts, stripping them of galvanization. It then melts the filler and proceeds with the brazing process.
Robotic Automation Results in Post-Processing Savings
One of the most appealing characteristics of laser brazing is how fairly easy it is to automate. The lasers used for brazing have a high beam profile and are extremely stable, allowing for well-controlled brazing. When the variability of a human operator’s touch is replaced with a robot’s ability to move the laser with precise movements, every brazed joint comes out the same.
As a result, automated laser brazing results in smooth, clean surfaces. This eliminates the need for post-processing, further reducing the number of labor hours needed. Workers no longer have to prepare the joint for painting or to apply the other corrosion-resistant coatings needed in aerospace. It can be cleaned and finished without any manual material removal.
Genesis Systems offers exceptional laser solutions that can automate your brazing processes and enhance material removal efforts.
Posted in Laser Welding, Robotic Applications, Robotic Welding