How Robotic Welding is Changing Heavy Fabrication
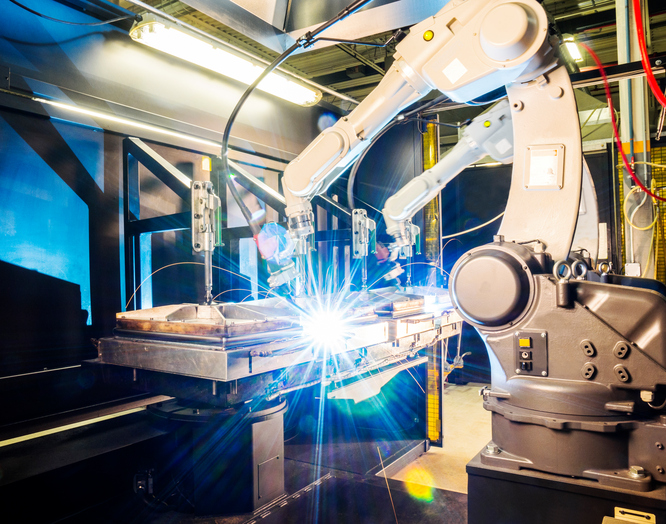
Historically, heavy fabrication processes have been mostly manual for a number of reasons. For one, robotic technology of the past simply could not keep up with the extreme demands of heavy fabrication applications, such as those found in the welding of construction vehicles, loader buckets or cutting of large plates. Robots were originally built for controlled environments, such as working on an assembly line in an automotive manufacturing plant.
Another main reason heavy fabricators haven’t used robotic welding and other automation technology is because of the cost of the initial investment, and wariness surrounding the time it takes to achieve return on investment (ROI).
Today’s robotic welding technology, however, is more than capable of automating most heavy fabrication processes while delivering ROI and gains in productivity.
The Robotic Welding Technology That’s Changing Heavy Fabrication
Over the years, robots have become more affordable, easier to use and far more commonplace for heavy fabricators. There are a few different technologies that have been drivers of this change.
Part Manipulation
One of the primary obstacles to automation has been securing, moving, and repositioning large, heavy parts. Now, custom headstock and tailstock positioners, along with several coordinated track-mounted welding robots, can lift and rotate parts that are several tons in order to automate the entire welding process. Even welding of long wall coal mining equipment, which can weigh in excess of 50,000 pounds, can be fully automated (read the case study here). Today’s robotic welding technology can reposition large, heavy parts to provide welding access to the entire part.
Smart Sensors
Smart sensors help compensate for material tolerances for processes like welding heavy steel. Parts like profiles, beams and tubes can distort from their correct dimensions during the welding process. A robotic welding system equipped with smart sensors for seam tracking allows the robot to adjust for this distortion during the welding cycle, maintaining weld accuracy even when dimensions change from what’s programmed into the robot. Material tolerances have always been a challenge to robotic welding, but today there is plenty of technology to account for part distortion.
Offline Programming
Most robotic welding systems today feature offline programming capabilities, which is a major appeal for heavy fabricators. A highly complex robotic welding system with track-mounted robots, part positioners, smart sensors and integrated software can be extremely difficult to program. In the past, this would significantly lengthen project delivery times and complicate maintenance, as most heavy fabricators did not keep programmers on staff. Today, offline programming allows robotic welding systems to start welding as soon as they’re installed on the factory floor, helping reduce the initial cost and time associated with automation investment, and reduces downtime when reprogramming is required.
Robotic welding capabilities are changing heavy fabrication. New robotic welding technology is capable of overcoming traditional obstacles to automation for large and heavy parts, and now heavy fabricators are undergoing a technological revolution.
To learn more on this topic, read Genesis Systems Group’s heavy industrial robotic integration case studies where heavy fabricators found ROI and productivity, even in the most challenging applications.
Posted in Robotic Welding