How Robotic Welding Creates Productivity for Manufacturers of Large Transportation Parts
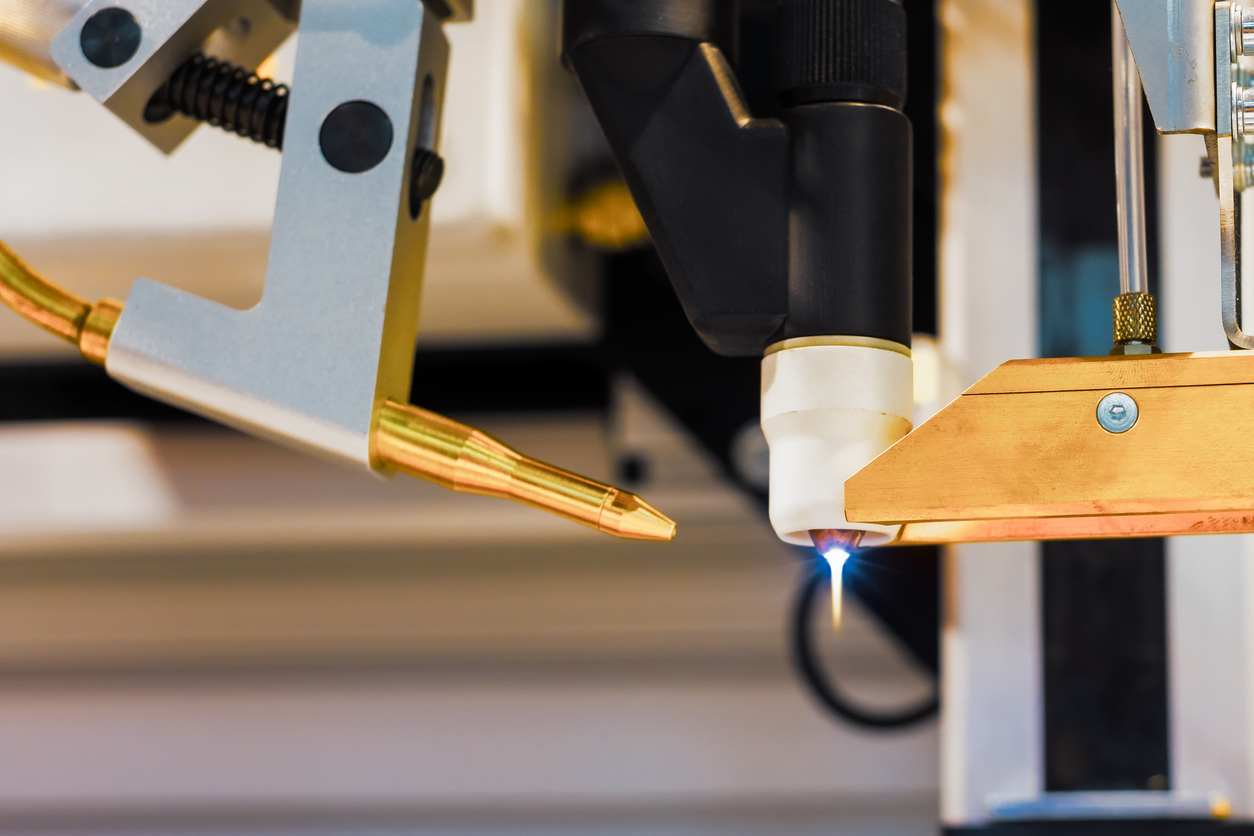
Robotic welding offers many benefits to manufacturers, particularly those that create large parts in the transportation industry. Typically, robotic welding is considered most effective for small, low mix parts with a high level of repeatability, but the most advanced, robotic welding work cells can productively handle large parts.
Often, these welding workcells are comprised of multiple robots with advanced robotic software and controls for consistent, quality welds. Compared to slower, error-prone and labor-intensive manual welds, robotic welding can deliver many productivity benefits.
Attributes of a Productive Robotic Welding Work Cell for Transportation Manufacturers
Many robotic welding workcells utilizing multiple robots for large parts involve extensive programming, often done offline before installation with robot simulation software, to avoid collisions while welding. The detailed programming of the robots also maximizes the reach of the arm – an important attribute for robots working on large parts.
Mobility is an important attribute of these kinds of robotic welding workcells, further extending the robots’ reach. Servo-driven tracks, mounted near or even above the part, allow one robot to reach more of the part than a typical stationary robot.
Delivering Robotic Welding ROI for a Tier-1 Transportation Manufacturer
Recently, a tier-1 trailer bed manufacturer was experiencing a high rate of defects and the manual weld process was slowing down production. They contacted Genesis Systems to install a custom, turn-key robotic welding system to solve their production challenges.
A two-station robotic welding design facilitated faster loading and unloading, which was previously a source of inefficiency. The extended reach of the two-robot system allowed for multiple welds to be made at the same time, improving both the speed and consistency of welding.
In the end, the robotic welding cell delivered quick ROI and sped up all welding processes for the trailer beds. Lead times were decreased and the overall cost of production was reduced.
To learn more on this topic, read the case study on Genesis’ robotic welding work cell for a tier-1 transportation manufacturer.
Posted in Robotic Welding