Robotic Welding Programming Challenges and Best Practices
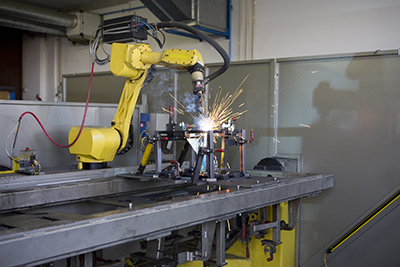
Manufacturers all over the world are speeding up production lines thanks to robotic welding. Not only do welding robots quicken the pace, but they offer an excellent return on investment. Thanks to this booming popularity, the need for robot programming in facilities where automation didn’t exist until recent years is ever growing.
Best Practices for Welding Robot Programming
OEMs often provide training and support on how to set up a new welding robot, but forward-thinking manufacturers know to plan out their welding automation solution before implementation.
One action a manufacturer needs to take first is to create an arc file library based on weld size. Each file should be clearly and accurately named. It’s wise to use corresponding numbers for the arc start and end files. It’s also smart for weave files to match arc files for each weld size for easy reference.
In addition, it’s good practice to keep weld programs small; less than 100 weld points typically is a good number, 200 maximum. Each weld in the process should be labeled with a line comment with any relevant information. Logical subroutines also help to keep program sizes manageable.
Manufacturers should also keep a master part to reference for robot programming. A marked-up part print works too. It’s a good idea to label the part with weld numbers and arc size file numbers. Doing so typically makes it much easier to adjust welds when necessary.
Keeping a log and backing up programs can reduce headaches when trying to figure out why a robot programming change was made. The log record should be kept in the robot’s workcell, so it’s easily accessible to reference. Workers should note the date, time, and reason for the change.
Challenges for Welding Robot Programming
Robot programmers have many obstacles to overcome, particularly for welding robotics. They must understand the principles of welding as well as the fundamentals of programming. They’re required to limit downtime resulting from programming changes in order to maintain the efficiency and productivity of the product line.
Robot programmers often have to know multiple software systems as they work with programming tools from more than one robot manufacturer. Programmers must plan where to position a welding robot’s joints and arm segments to account for changes in arcs and joint angles. Many welding results must be tested by trial and error, requiring extensive experience to master robot programming.
Looking to the future, new robot accessories are being developed to assist with robot programming. As an example, one new accessory simplifies the training process by allowing a robot programmer to move a welding robot arm through its workflow. Welding parameters are adjusted on the fly via a touchscreen interface and can be tested immediately. Keeping up with the latest accessory options and evaluating which can work for your organization can be very beneficial.
Find custom and turn-key robotic welding solutions that cut cycle times, produce quality welds, and reduce post finishing processes on our site.
Posted in Robotic Systems Integrator, Robotic Welding